MFL Training
Magnetic flux leakage (MFL) training and inspection services for steel structures
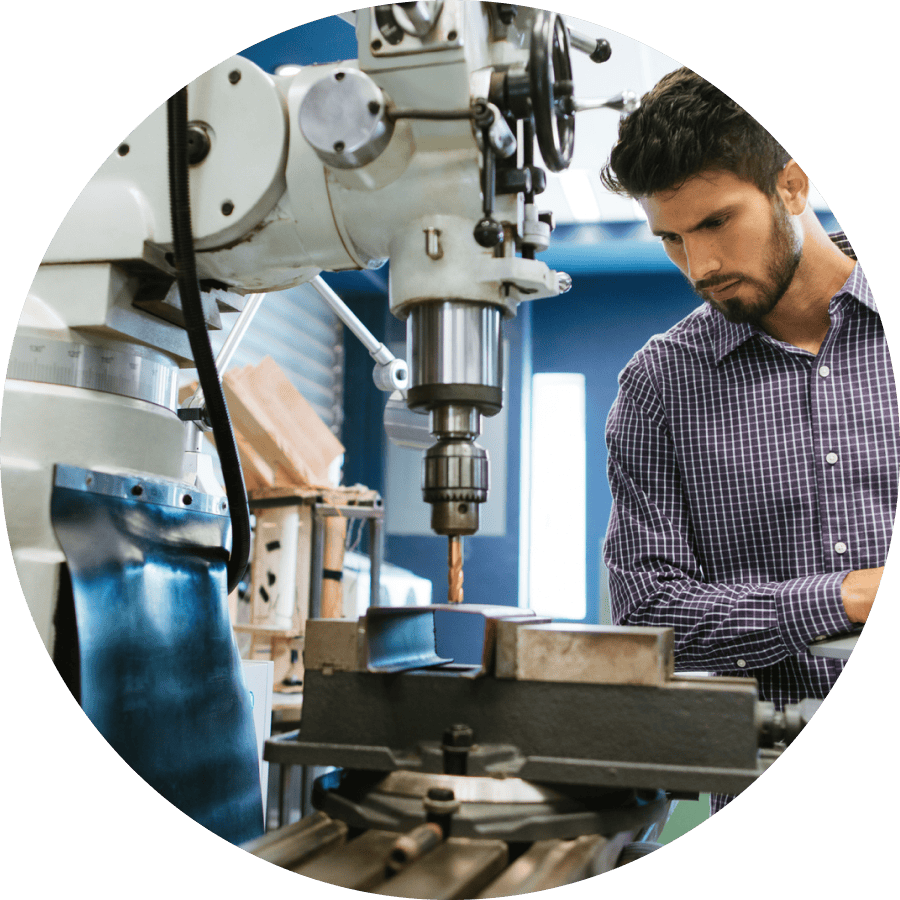
Unveiling hidden damage with magnetic flux leakage testing
- Corrosion: MFL excels at detecting areas where corrosion has thinned or weakened the steel structure.
- Pitting: Localized areas of material loss due to corrosion can be effectively identified using MFL technology.
- Wall loss: MFL sines in revealing overall reductions in the wall thickness of the steel structure, a critical indicator of potential integrity issues.
How magnetic flux leakage works
- Magnetization: A powerful magnet temporarily magnetizes the steel structure.
- Leakage detection: Any defects such as corrosion or wall loss disrupt the magnetic field, causing it to "leak" from those areas.
- Sensor measurement: Strategically placed magnetic sensors detect these leakage fields, measuring their strength and direction.
- Defect identification: The 3D distribution of the leakage field, measured by multiple sensors, helps pinpoint the location and nature of defects in the steel.
Advantages and limitations of magnetic flux leakage
MFL training equips inspectors with the knowledge and skills to leverage this technology effectively. While MFL offers a range of advantages, understanding its limitations ensures it's the right tool for the job.
Advantages
High sensitivity:
MFL excels at detecting even small defects such as pits as shallow as 0.1 mm in carbon steel structures. This makes it a valuable tool for ensuring the integrity of critical assets.
Reliable results:
MFL testing produces consistent and repeatable results, minimizing the risk of errors or misinterpretations.
Reduced skill dependence:
Compared to some NDT methods, MFL requires less operator expertise for basic operation. However, proper interpretation of results still benefits from training and experience.
Versatility:
MFL can be effectively used on various geometries, including fin tubes, expanding its range of applications.
Efficiency:
MFL inspections are known for their ease of operation and efficient data collection.
Limitations
Saturation requirement:
Accurate MFL testing relies on achieving complete magnetic saturation of the steel wall. This might not always be feasible, especially in thicker structures.
Signal differentiation:
MFL cannot distinguish between top and bottom side defects within the steel wall. Advanced techniques might be necessary for such differentiation.
Inspection length:
Axial (lengthwise) inspections of very long and narrow sections might be limited by the MFL equipment's design.
Quantitative challenges:
While MFL can detect defects, it might not always provide precise measurements of their depth or severity.
Susceptibility to interference:
The magnetic field used in MFL can be influenced by variations in the pipe wall thickness, requiring proper calibration and data analysis techniques.
Real-world applications of magnetic flux leakage
MFL has emerged as a vital NDT method in various industries mainly for its ability to efficiently detect corrosion, pitting, and wall loss in steel structures. Here are its most common applications:
Ensuring aboveground storage tank integrity
The oil and gas industry heavily relies on MFL for inspecting aboveground storage tanks. This rapid and reliable technique allows for the timely detection of defects such as corrosion and wall thinning, ensuring the safe storage of critical resources.
Streamlining inspections in petrochemical facilities
Petrochemical facilities utilize MFL for high-speed inspections of storage tanks and carbon steel pipes. This efficiency minimizes downtime and maintenance costs while upholding safety standards.
Inspecting finned tubes for optimal performance
MFL's versatility extends to inspecting finned tubes, commonly found in heat exchangers. By identifying potential defects in these intricate components, MFL helps maintain optimal heat transfer and prevent costly equipment failures.
Other Services
Explore our comprehensive suite of NDT training services
We offer a complete suite of services for program establishment, audits, and examinations.