Liquid Penetrant Testing Training (PT) and Certification
Master PT skills and obtain certification through NDT-CGI's expert programs
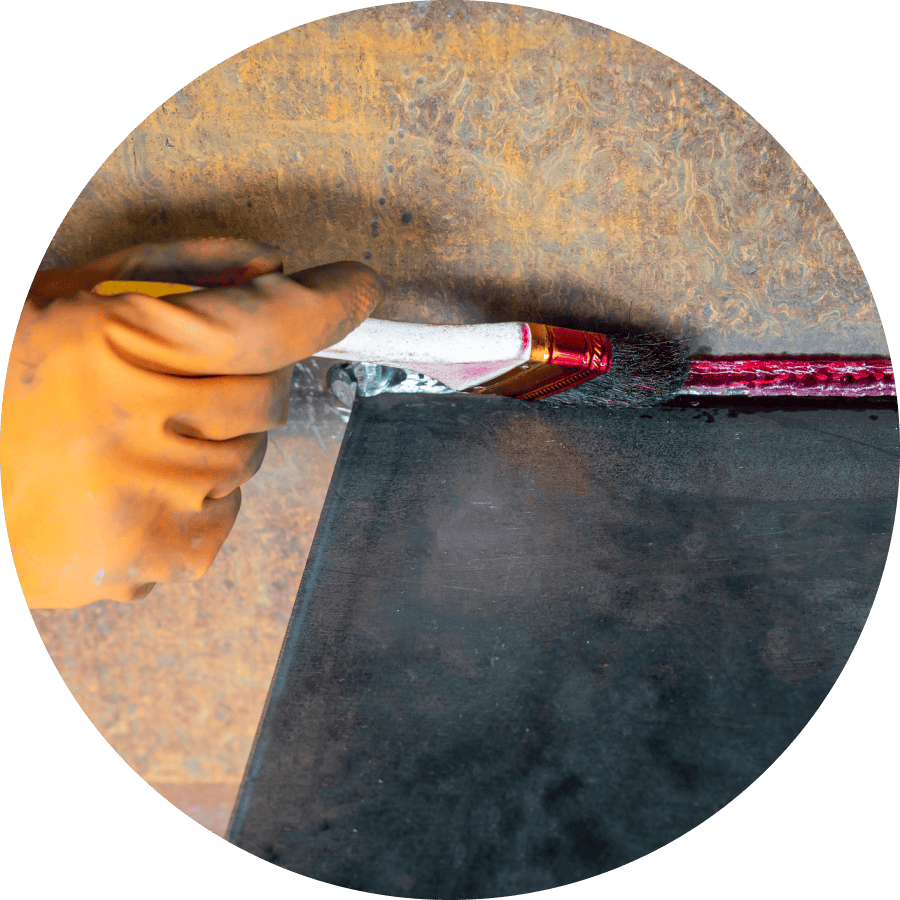
Understanding liquid penetrant testing
- Casting and forging flaws: These include cracks, porosity, and other imperfections introduced during the casting or forging processes.
- Welding defects: These are imperfections like cracks or incomplete fusion in welded joints.
- Leaks in new products: PT helps ensure the integrity of newly manufactured components by detecting leaks before they become a problem.
- Fatigue cracks: This NDT method can reveal cracks that develop in service due to repeated stress or vibration.
The versatility of liquid penetrant testing
Liquid penetrant testing training: Flexible solutions to meet your needs
Liquid Penetrant Testing Level I Topical Outline
- 1. Introduction
- Brief history of nondestructive testing and liquid penetrant testing
- Purpose of liquid penetrant testing
- Basic principles of liquid penetrant testing
- Types of liquid penetrants commercially available
- Method of personnel qualification
- 2. Liquid Penetrant Processing
- Preparation of parts
- Adequate lighting
- Application of penetrant to parts
- Removal of surface penetrant
- Developer application and drying
- Inspection and evaluation
- Post-cleaning
- 3. Various Penetrant Testing Methods
- Current ASTM and ASME standard methods – ASTM E 165, E 1208, E 1209, E 1210 and E 1417
- Characteristics of each method
- General applications of each method
- 4. Liquid Penetrant Testing Equipment
- Liquid penetrant testing units
- Lighting for liquid penetrant testing equipment and light meters
- Materials for liquid penetrant testing
- Precautions in liquid penetrant inspection
Liquid Penetrant Testing Level I Topical Outline
- 1. Review
- Basic principles
- Process of various methods
- Equipment
- 2. Selection of the Appropriate Penetrant Testing Method
- Advantages of various methods
- Disadvantages of various methods
- 3. Inspection and Evaluation of Indications
- General
- Discontinuities inherent in various materials
- Reason for indications
- Appearance of indications
- Time for indications to appear
- Persistence of indications
- Effects of temperature and lighting (white to UV)
- Effects of metal smearing operations (shot peening, machining, etc.)
- Preferred sequence for penetrant inspection
- Part preparation (pre-cleaning, stripping, etc.)
- Factors affecting indications
- Pre-cleaning
- Penetrant used
- Prior processing
- Technique used
- Indications from cracks
- Cracks occurring during solidification
- Cracks occurring during processing
- Cracks occurring during service
- Indications from porosity
- Indications from specific material forms
- Forgings
- Castings
- Plate
- Welds
- Extrusions
- Evaluation of indications
- True indications
- False indications
- Relevant indications
- Nonrelevant indications
- Process control
- Controlling process variables
- Testing and maintenance materials
- 4. Inspection Procedures and Standards
- Inspection procedures (minimum requirements)
- Standards/codes
- Applicable methods/processes
- Acceptance criteria
Advantages and limitations of liquid penetrant testing
PT is considered a foundational NDT technique, primarily because it is straightforward, provides quick results, and is efficient in revealing surface imperfections in diverse industrial settings. While PT offers numerous advantages, it's crucial to understand its limitations to ensure it's the right testing method for your specific needs.
Liquid penetrant testing training and certification equips inspectors with the knowledge and skills to leverage PT's strengths while mitigating its limitations.
Advantages
High defect visibility:
PT excels at revealing surface defects with exceptional clarity, making these defects readily identifiable by the inspector.
Cost-effective and efficient:
PT is a relatively inexpensive NDT method and offers rapid turnaround times, minimizing inspection costs and downtime.
Field-ready portability:
The portable nature of PT equipment allows for inspections to be conducted virtually anywhere. Battery power options further enhance flexibility, making PT suitable for field applications.
Material versatility:
PT can be effectively used on a wide range of materials, including ferrous and non-ferrous metals, as well as ceramics and some plastics.
Limitations
Surface inspection only:
A key limitation of PT is its inability to detect defects below the surface. For deeper inspections, other NDT methods such as magnetic flux leakage might be necessary.
Surface roughness challenges:
Rough surfaces, such as those found on as-fabricated welds, can pose challenges during PT. Removing excess penetrant from these surfaces can be difficult, potentially leading to misinterpretations of test results.
Temperature sensitivity:
PT penetrants typically perform best within a specific temperature range. While specialized procedures and penetrants exist for extreme temperatures, their application requires additional qualification steps.
Material porosity dependence:
Highly porous materials may not be suitable for PT, as the penetrant can seep into the pores and obscure relevant surface defects.
Other Services
Explore our comprehensive suite of NDT training services
We offer a complete suite of services for program establishment, audits, and examinations.